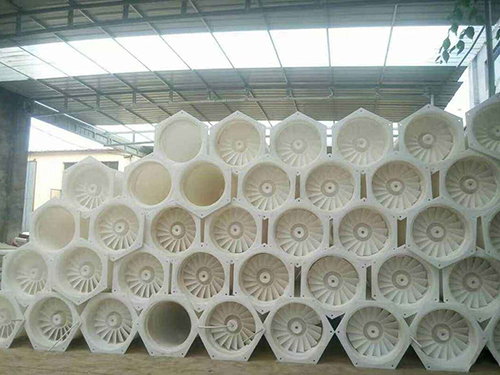
在旋汇耦合湿法脱硫技术中,烟气通过旋汇耦合装置与浆液产生可控的湍流空间,提高了气液固三相传质速率,完成一级脱硫除尘,同时实现了快速降温及烟气均布。引风机出口烟气进人脱硫吸收塔,经过旋汇耦合装置,根据流体动力学原理,形成强大的可控湍流空间,使气液固三相充分接触,提高传质效率,同时液气比比同类技术降低30%,并同时实现高效脱硫和除尘。旋汇耦合装置适用于不用工艺、不同工况、不同煤种、脱硫原料的不同粒径,可应付2万mg/Nm³以内二氧 化硫含量的烟气处理系统,完成高效脱硫过程,效率可达99.5%以上。
基于增强气液传质机理的旋汇耦合湿法脱硫技术是 一项简洁、适应性强的实用性技术,可广泛应用于对旧脱硫系统的提效改造,改造周期短、工程量小、不改变吸收塔外部结构、不改变原系统运行方式。在对旧脱硫项目进行旋汇耦合改造时,仅需在原吸收塔喷淋层下方增加旋汇耦合器层,该设置荷载小,针对现有机组脱硫塔的改造基本无需增加加固结构。且旋汇耦合改造几乎不涉及电气热控设备的增加,可视为塔内固定原件使用,不增加运行负担。
河南华润首阳山电厂一期2x630MW超临界燃煤机组于2006年投运。脱硝装置采用选择性催化还原法(SCR)脱硝技术,每台机组装设2台脱硝反应器,脱硝装置按“2+1”布置,催化剂采用蜂窝式。原除尘装置采用兰州电力修造厂生产的双室四电场除尘器。脱硫装置采用石灰石-石膏湿法技术,按一炉一塔设计。脱硫装置2013年进行引增合一,拆除增压风机,脱硫废水改为以事故浆液箱为沉淀箱,清水排至化学工业废水处理系统的方式进行处置。为响应国家燃煤电厂烟气超净排放号召,该电厂于2015年5月对脱硫系统进行了旋汇耦合脱硫技术改造,要求改造后二氧 化硫排放浓度不大于35mg/Nm³(标态、干基、6%O2)。改造过程分别对吸收塔系统、烟气系统、石膏脱水系统进行了优化改造,并加装了管束式除尘除雾器、更换了净烟气烟气污染物连续监测装置的测点位置。改造后的设计煤种按照收到基含硫量1.0%考虑,脱硫人口二氧 化硫浓度为2564mg/Nm³(标态、干基、6%O2)。吸收塔系统改造过程中,主要内容为原吸收塔加装了旋汇耦合装置、更换了原喷淋层。该项目于2015年8月完成,由国家电网河南省电科院执行环保系统验收。验收结果显 示,在机组接近满负荷的工况下净烟气二氧 化硫浓度仅16.1mg/Nm³(标态、干基、6%O2),脱硫系统-完成超净排放任务。且在投运以来,脱硫系统工况稳定、高效、经济,受到业主的高度肯定。
旋汇耦合湿法脱硫技术拥有50MW、200MW、220MW、300MW、330MW、600MW及1000MW等170余台大中型燃煤机组烟气脱硫项目业绩,其中于2015年(国家相关部门提出超净排放要求)后完成建设或改造的机组均达到超低排放。
泊头市帅源环保设备有限公司(http://www.shuaiyuanhb.com)系一家专业研发、设计、制造、安装及售后为一体的高效除雾除尘设备厂家,公司主要经营管束除尘除雾设备,多级除尘除雾器,多管高效除雾除尘器及多种除尘器设备与除尘器配件等配套设备