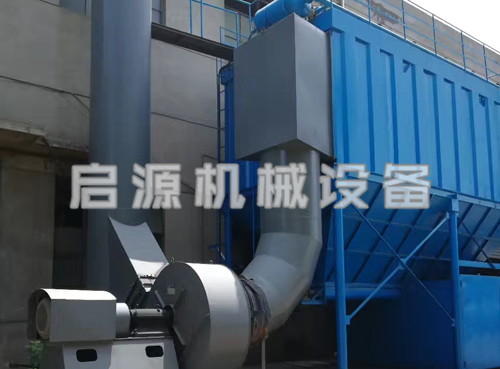
目前电炉烟气冷却的方式有水冷+机力风冷、废钢预热+水冷、水冷+热管余热锅炉等。
1、水冷+机力风冷
水冷+机力风冷系统的流程。电炉第四孔出口的高温烟气进入水冷烟道,同时,混入从电炉四孔水冷弯头和水冷滑套间的缝隙吸入的空气,进行燃烧,之后进入燃烧沉降室,在燃烧沉降室进行燃烧和灰尘沉降后,从燃烧沉降室出来的高温烟气经过水冷烟道冷却到600℃左右,进入机力风冷器,冷却后的烟气与电炉密闭罩的除尘烟气混合降温后进入布袋除尘器除尘,之后通过目前国内外有大量电炉烟气采用水冷方式的案例。例如2006年投产的太原钢铁(集团)有限公司1座160t电炉,2009年投产的日本新日铁1座100t电炉,2009年投产的印度EASSR公司2座180t电炉,均采用了水冷烟道冷却烟气的方式。水冷烟道具有一次投资少、技术可靠、运行稳定的特点,所以目前还在大量应用。该方式最大的弊端就是 烟气中大量的显热无法被利用,浪费了能源,增加了冷却水的消耗量,同时工业水的循环又消耗大量的电能。
2、废钢预热+水冷
电炉专用除尘设备烟气冷却的另一种方案为废钢预热+水冷。先利用电炉烟气预热废钢,之后800~500℃的高温烟气再经过燃烧沉降室、喷雾冷却器冷却后进入布袋除尘器,其后续工艺和水冷+机力风冷相同。
因此该种方式也存在较大部分烟气余热未利用,喷入大量冷水,增加除尘负荷等问题。同时该技术在二噁英排放、废钢预热效果等方面仍存在问题。
3、水冷+热管余热锅炉
该方案中,机力风冷器前流程与水冷+机力风冷相同,仅以热管余热锅炉替代机力风冷器,将原来通过机力风冷器排放到大气中的余热加以回收利用,产生蒸汽。2006年投产的山钢集团莱芜钢铁集团有限公司50t电炉余热回收系统便属于该种形式。
该方案的缺点主要是 在建设余热锅炉系统时,仍需建设庞大的水冷系统,回收的热量有限,仅回收部分(约800一250℃)的烟气余热。另一个问题是 热管余热锅炉的换热效率随时间下降很快。某钢厂100t电炉余热锅炉采用热管形式,投产初期冶炼期内蒸汽回收量8t/h,3年左右下降到3.5t/h。同时由于常用的碳钢一水重力热管本身结构的原因,温度过高会引起其内部HZ的积累,热管锅炉进口温度一般要求低于850℃,这样使得热管余热锅炉的压力很难提高,一般情况下其出口蒸汽压力小于2.0MPa,蒸汽的利用较为困难。
泊头市启源机械设备制造有限公司(http://www.btyhjs.com)主营项目: 无机浸渗设备、低温等离子空气净化器、热制芯车间废气处理设备、焦化厂地面站除尘器产品已浸透到华北、西北、华南、东北的铸造行业,深受到业内专家的好评,用户的亲睐。